SMART PRODUCT: THE DIGITAL TWIN OPTIMIZING MDF PRODUCTION
In its commitment to a smart and sustainable factory, FINSA is leading the development of a smart product capable of anticipating problems, optimizing resources, and ensuring quality in MDF board manufacturing. With the support of expert entities such as Gradiant and the University of Santiago de Compostela (USC), this challenge focuses on creating a digital twin of the product and process: a virtual replica that simulates, in real time, what happens on the production line.
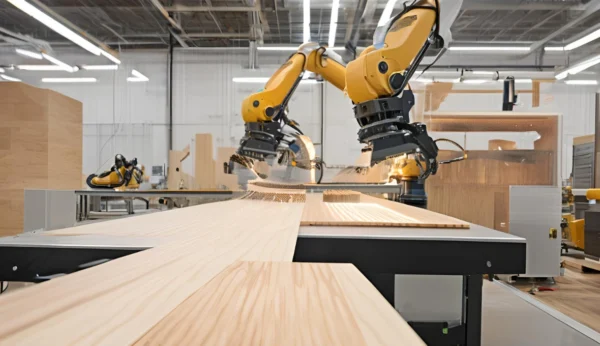
Eliminating trial and error in production
The main goal is to design a robust digital architecture that integrates sensors, AI models, and historical and real-time data. This will enable process monitoring, prediction of critical variables such as moisture or density, anomaly detection before they impact the product, and improved quality control without the need for destructive testing.
Among the expected outcomes is the implementation of five pilot demonstrators at the Padrón, Orember, and Santiago factories, which will validate the potential of this technology in real-world scenarios:
- A system for detecting anomalies in industrial data, sending real-time alerts when signals could compromise production.
- An advanced process variable prediction system, integrated with a graphical interface to support decision-making.
- Predictive models applied to the product, enabling quality assessment of each board directly on the production line, reducing defects and waste.
- A real-time raw material cost estimation module.
- A demonstrator for the melamine impregnation oven, modeling thermal flow and improving paper curing.
This development not only enhances the efficiency and sustainability of the process but also positions the Galician wood industry at the forefront of Industry 4.0.